Structural Marvels
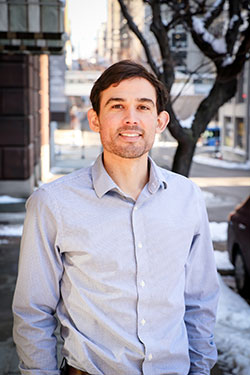
“People who are even a little familiar with bridge engineering aren't necessarily aware of what we're doing behind the scenes,” said Josh Crain.
Crain is an associate senior structural engineer at Genesis Structures, a structural engineering consulting firm specializing in bridge and architectural erection engineering and structural design. For the last 13 years, Crain has been doing that behind-the-scenes work in on-site bridge engineering – which includes moving gigantic bridge spans upriver with tugboats, executing time-sensitive projects that must be completed within a very narrow window of time, and orchestrating demolition with precision. The behind-the-scenes work is where innovation and craftsmanship meet.
Civil Engineering Mentors
Crain developed his interest in engineering from the family business. His dad and brother ran a business that did light construction when he was growing up. In high school, due to with his familiarity with the family trade, Crain naturally gravitated toward engineering. Construction engineering and civil engineering, specifically structures, drew him in.
When he started at KU, he took the freshman course called “Intro to Civil Engineering,” an overview of the different areas of civil engineering. Meeting engineering professionals from different disciplines reinforced his interest in working with structures.
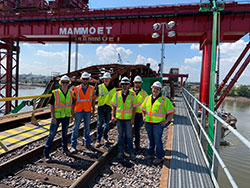
During his undergraduate years, while leading the Steel Bridge Team at KU, he struck up a good relationship with steel bridge faculty advisor Professor Caroline Bennett. She gave him the opportunity to go to graduate school, where Crain worked with her on bridge-focused research.
Dr. Bennett was one of his mentors, along with Dr. Stan Rolfe, who has since passed.
“Both Dr. Bennett and Dr. Rolfe helped guide me in my undergrad years and encouraged me to go to graduate school, which is the big reason why I'm at a firm like Genesis,” Crain said. “The extra courses I took during graduate school were very beneficial for me early in my career, so I definitely credit them with steering me in the right direction.”
While earning his bachelor’s and master’s in civil engineering from the University of Kansas, Crain put in time in internships, research, and teaching assistantships. After graduating, he joined Genesis Structures as a structural engineer for temporary works projects.
Currently, his biggest mentors at this point are the two principals at Genesis, Dave Byers and Dave Rogowski. “They're both really good at what they do, good leaders, technically sound, and great at relating to clients. They’ve molded me to where I am now.”
Erecting the Burlington River Bridge in Burlington, Iowa
Bridges are incredibly immense and complex structures, not only in the design but also in the extensive logistics necessary to get them safely built or erected. “We deal with projects that require specialty engineering to ensure safety during construction,” explained Crain. “We are talking about bridges that weigh in the millions of pounds, so we are working on a tremendous scale.”
One of Crain’s earliest jobs was replacing seven 300-foot BNSF approach truss spans over the Mississippi River at Burlington, Iowa.
Having a bridge closed costs railroads so much money, that paying for substantial temporary works engineering is actually more economical.
“Some of our change-outs consist of ‘Get the old bridge out, do what we need to do to the piers, put the new bridge in,’ so it happens very fast,” Crain said.
As a result, the Burlington bridge project involved several 36-hours closures – and two of the new 300-foot spans had to be completely installed within that space of time.
Naturally, extensive planning must take place well beforehand for projects of this scope. “The bridge is often in its most vulnerable state as it’s being built or removed, so we do a lot of modeling and a lot of studying to make sure that the structure is going to be able to be put together safely.” Logistics and extensive planning also be covered in this time.
“For Burlington, we built the new bridges in their entirety on a barge and brought each truss to where it's going to be in its final resting place,” Crain said.
So when it came time for a new section to be brought in, they closed the track for 36 hours and got to work.
“It's exciting when it happens and when it goes well,” Crain said, “because there's so much time and energy put into it.”
Replacing the Merchants Bridge in St. Louis
More recently, Crain was part of a team that rapid-assembled the Merchants Bridges in St. Louis, a 45-month railroad project.
Crain was particularly proud of this project. “As I'm advancing in my career, I'm getting a longer and longer leash as it comes to responsibility. That was one of the first projects where, ‘Man, I really gotta take the ball and run with it,’ which made it more exciting.”
The three Merchants trusses, each 550 feet tall and weighing 9 million pounds, would be tricky to change out on any body of water, but the whole operation was made even more complex by the Mississippi River’s rushing water.
For the Merchants project, each truss was completely pre-assembled off alignment on barges, then tugboats would push the barge to the work area. Once there, the tugboats would maneuver it into place, then hold it steady against the current. The truss would be picked up with strand jacks supported on an overhead gantry beam that lift it up off the barge. The bridge sections were raised and set onto sleds on a temporary frame. Then the sections were slid onto the permanent supports.
“The river's not exactly the best place to push a bridge on a barge,” Crain said. “This part of the Mississippi had really high stream flow, so we had to provide about 14,000 horsepower of tugboats just to keep the structure from going downstream.”
The Importance of Demolition Safety
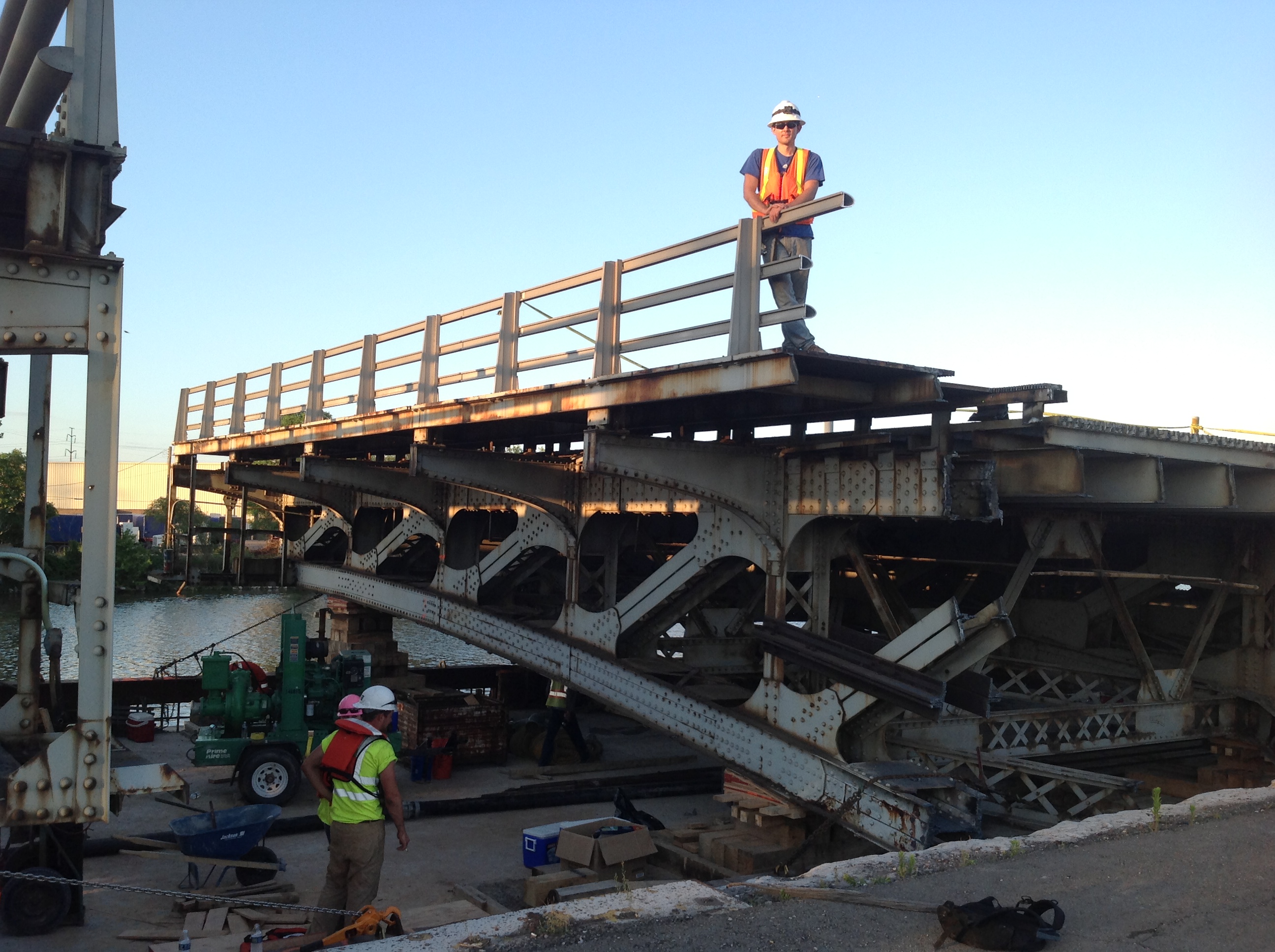
Lately, Crain has been focusing more on safety in demolition. The Bridge Demolition Subcommittee within the ASCE Construction Institute Temporary Words Committee, of which Crain is a member, has completed their final draft on a first-of-its-kind best-practices document for demolition engineering. The Bridge Demolition Best Practice document is currently under review from ASCE Publishing and should be available next year. Crain stated that there needed to be more minimum standards and guidance for maintaining a safe structure as a bridge is being demolished.
At Genesis, Crain’s team analyzes structures of all kinds being dismantled, including those that are removed with explosives. Contractors strategically weaken the structure by making the pre-cuts (which allow the bridge to break at specific points) and put explosives charges at the cut locations called shape charges. Explosives are a quick and sometimes safter way to take down a bridge.
“The alternative to explosives is not quite as exciting,” Crain said. “It’s just putting equipment on top of the bridge, knocking the deck out, and pulling out the steel beams with the crane or equipment on the ground – basically building a bridge in reverse.”
Regardless of how bridges are taken down, demolition plans require careful planning and execution to ensure the work is done safely.
New Challenges, New Structures for the Future
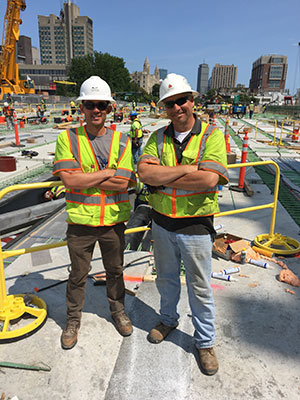
Crain enjoys working on any project that brings new challenges. Recently he’s been working on the erection of several long-span arch bridges. “Those are fun just because they're a geometric challenge,” he said. “They're not easy to build, so there's a lot for us to do, but they result in beautiful structures. I would say that some of these arches are my favorite projects – but they're not done yet, so I don't want to jinx them!”
He will be teaching a course at the KU Edwards campus this fall on the design of temporary works.
The best part of Crain’s work is looking at his finished projects.
“It’s sometimes stressful,” he admitted, “but it's also satisfying to get that gratification of being able to see that what you engineer actually works. You're designing for real loads, and you get to see the results immediately. Being able to see your work in person is really satisfying.”